Written on the front:
On October 29, the Germany Chancellor Angela Merkel arrives in Beijing, opened its decade's eighth visit to China since he took office.
Accordingly the former Germany Embassy introduced during their stay in Beijing, Merkel will meet with Chinese leaders, analysis discussed in October last year in Berlin, the third round of negotiations between the Government and the two countries issued the Sino-German cooperation in implementation of the platform for action. Among them, the industry 4.0 discussions is expected to be the top priority.
German industry at the national level 4.0 partnerships beginning in 2014. In October of that year, Premier Li keqiang in Berlin with Merkel, after intensive consultations, jointly published the platform for action for Sino-German cooperation, announced that the two countries will carry out industrial 4.0 partnerships. Industry insiders believe, German industry 4.0 strategic cooperation framework, showing strong support of senior manufacturing 4.0 upgrade, industry has risen to 4.0 a national strategic level.
Industrial 4.0 as a concept that represents the future development direction of advanced manufacturing industry. The concept of Germany raised the industry's first, from 2011 the Hannover industrial fair, initial ideas through media such as the Internet of things to raise Germany manufacturing. Two years after the Hannover industrial fair, by the "academia," made up of Germany "industrial 4.0 Workgroup" published, entitled the Germany industrial 4.0 recommendations on the implementation of the strategic plan, said Internet and manufacturing services declared the fourth industrial revolution to come.
Implementation of recommendations is described industrial 4.0: in intelligent factory of the future, and can communicate with humans, machines and resources, just as natural as social networks. Intelligent product "knows" the details of how they were produced, and their use. They will take the initiative to the manufacturing process, and answer questions such as "when I was making", "to deal with me which parameters should be used", "where I should be sent to" and so on.
Known as Germany manufacturing top of Siemens, 4.0 is industry pioneer. Siemens Amberg electronics manufacturing factory, is Europe's and the world's most advanced digital factory, is considered the closest industrial 4.0 concept prototype plant. Worth noting is that the Merkel visit, President and CEO of Siemens AG Kay SA will also accompany.
168-year history of Siemens can almost be seen as a microcosm of the modern industrial processes. From a small workshop to develop so far, Siemens has created the industrial Empire had become "Germany" made synonymous with doing my part.
From the pointer Telegraph started to the aorta of businesses on information technology, Siemens stepped on to electric power, key nodes of information marked the first two industrial revolutions. Industrial physics based on information fusion system 4.0 concept was born early, Siemens again smelling the scent of a new round of industrial revolution. Aimed at real networking, and cloud computing, and big data, and industrial Ethernet, technology, Siemens integrated has currently global most advanced of production management system, and production process software and hardware, as Siemens manufacturing implementation system (MES) software Simatic IT, and Siemens products life cycle management (PLM) software, and industrial design software (Comos), and full integrated automation (TIA), and full integrated drive system (IDS), and so on.
Industrial 4.0, Germany what has the genius? To this end, surging journalists visited Siemens Germany Amberg electronic manufacturing plant in the East of Bavaria.
Exploration camp Siemens Amberg manufacturing plant
Amberg electronics manufacturing plants (EWA) from the appearance point of view is not cool, three workshop square, with its red brick facade, appearing in a simple, low-key 890 industrial style of the last century. In fact, since 1989 the factory, after 26 years, Amberg fixed electronic manufacturing plant in appearance.
However, in this appearance and the number of workers remained intact, even within the factory of production area has not increased, one industry 4.0 direction evolution never stops. Today, the plant's capacity from 26 up to 8 times times the Simatic products can produce about 12 million per year, according to an annual production of 230 days, which means that in every seconds to produce a product.
Product quality is significantly improved compared with 1989 the per process error 500 million electronic products, now an error rate of only 12 times, equivalent to increase 40 times times the mass.
Professor Karl-Heinz b u ttner, head of the factory said, "as far as I know, no comparable factory in the world with such a low defect rate. "
At present, Amberg electronic manufacturing plant can produce over 1000 kinds of products, including Simatic programmable logic controllers (PLC) and related products. These products are used to control machinery and factories, to automate the production process. Simatic products control cruise ship-borne system can also be used in industrial manufacturing processes, such as the automotive industry, can even be used to control the ski cable car.
The factory is the most amazing: not only the production of products, and collect and process large amounts of information. Inside, chest-high gray-blue Cabinet line, placing the monitor, data flows like waterfall down. Indicator light is flashing red and green light, whole workshop in long rows at bright and cold light halogen lamp. Employees in blue uniforms, walked quietly without interest in the clean blue-and-white marbled on PVC floor.
In order to accurately collect data, Amberg factory of more than 300 million component has its own "identity". These basic identification information including: which lines of production, what material, how much and what kind of screw Torque is used. When when an element enters the oven, the machine will determine what length, temperature and time, and next to the oven components which can be judged, timely adjust production parameters. In the process, Simatic IT manufacturing execution systems will generate about 50 million production process information and store.
Through displays, information workers can check out the day's production process, and to uncover short Board in the production, such as which part is high probability for the problem. After a series of further analysis and allows producers to the entire production process of the relevant variables, have a better understanding, thereby reducing product defects rate.
Is different from the ordinary factory Amberg need is to know how to use software to control complex processes and qualified employees. Workers no longer wears overalls manufacturing quality products, their current tool is a touch screen, and Tablet PCs.
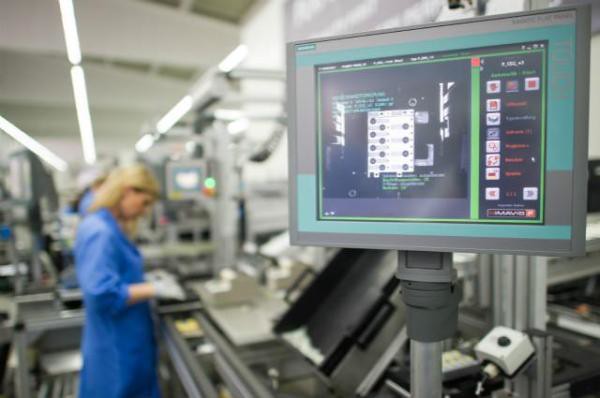
Amberg in electronic manufacturing plant, all process control and optimization of IT systems, ensuring 99.9988% the product qualified rate.
In electronic manufacturing plant of Amberg, real virtual factory and factories running real factory data parameters, production environment are reflected through a virtual factory, and the virtual factory to handle the real factory. Among them, nearly 75% of the production that the job is automating. Products can communicate with the production equipment, IT systems and optimize all processes, ensuring 99.9988% the product qualified rate.
Done by the human parts, only the beginning of the production process, namely employees will be the initial component (bare circuit board) placed on line links, was performed by a human. Since all operations are automatic. It is worth mentioning that, Simatic unit Simatic control unit production. Production has been shipped to from the beginning, the entire production process uses a total of 1000 such control devices. SFC opening external funding tickets: four futures
Amberg electronics factory is a Siemens "digital business platform" model. "Digital business platform" is a kind of production environment, will become standard in the next 10 years. In this environment, free to control its own process. In other words, the production codes tell machines what they require, followed by which production processes must be performed. The system was built "industrial 4.0" take the first step.
4.0 but this industry's portrayal of "seamless digital and physical world" scenes, there is still a big gap. "If the industry 4.0 still in the age of 20, then Siemens has now reached ' industry 3. X'。 "This is the Member of the Management Board of Siemens AG, Ruth wolusiwo, Chief Technology Officer (Siegfried Russwurm) self scoring.
In the fourth industrial revolution in vision, integration of real and virtual production environment. By then, factories will, to a large extent, self control and optimization, because their products can interact and communicate with production systems, to optimize the production process. Products and machines will be determined, in order to deliver, should be first in line to complete operation. Known as software agents, independent computer program will monitor every process that is running, ensure compliance with production rules.
No comments:
Post a Comment